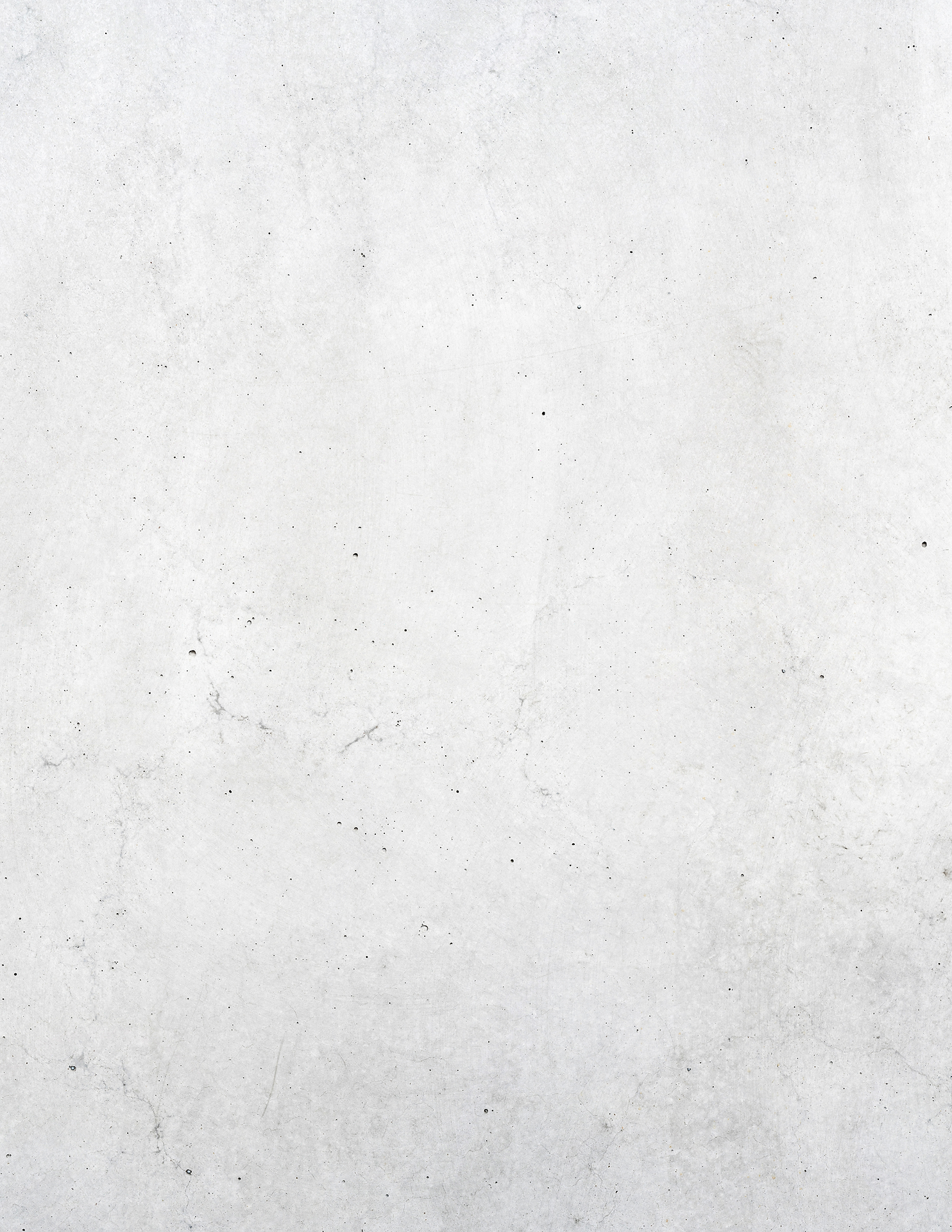
The IGGA offers the following fact sheets on pavement surfacing techniques and preservation/repair methods. Select the application(s), preservation/optimization technique(s) or pavement criteria/issue(s) to browse the fact sheets, or use the search function.
No results found. Please try another combination of categories.
No results found. Please try another combination of categories.
Concrete Pavement Preservation and Diamond Grinding: What makes diamond grinding and CPP environmentally friendly?
Concrete pavement preservation (CPP) and diamond grinding are longstanding preservation techniques that contribute to sustainable infrastructure by significantly reducing environmental impact while enhancing safety and performance.
Application(s)
Bridge, City/Municipal, Highway
Technique(s)
Diamond Grinding, Concrete Pavement Preservation and Restoration
Issue(s)
Quick Facts: Pavement Base and Subgrade Repair
Subgrade repair comes in several forms, including slab stabilization (aka, undersealing and sub sealing), slab jacking, and medium and deep injection grouting. Subsurface restoration maintains the structural integrity of the slab and reduces pumping, faulting, and cracking.
Application(s)
Airport/Airfield, City/Municipal, Highway, Industrial, Race Track
Technique(s)
Slab Stabilization
Issue(s)
Structural/Material Issues
Quick Facts: Joint Resealing
Joint resealing protects pavement joints from water and incompressible. Uncontrolled water ingress, especially water from a pavement’s surface, can lead to spalling, base or subgrade softening, dowel bar corrosion, pavement joint blow-ups and/or materials-related distress. Performed alone, joint resealing is a maintenance activity. However, it is also an important part of the Concrete Pavement Preservation (CPP) toolbox.
Application(s)
Airport/Airfield, City/Municipal, Highway, Industrial, Race Track
Technique(s)
Joint and Crack Resealing
Issue(s)
Structural/Material Issues
Quick Facts: Safety Grooving: Grooving runways reduces hydroplaning
Water, slush or wet snow on a runway surface can cause aircraft to skid upon landing. Runway diamond grooving is a time-and cost-effective way to rehabilitate older runways that are showing loss of friction. Diamond saw blades can be used to create grooves in both portland cement concrete (PCC) pavement and hot mix asphalt pavement.
Application(s)
Airport/Airfield, Bridge, City/Municipal, Highway, Industrial, Race Track
Technique(s)
Diamond Grooving
Issue(s)
Friction/Safety
Quick Facts: Safety Grooving: Grooving roadways decreases accidents and saves lives
Diamond grooving machines with circular diamond-tipped saw blades are used to saw grooves into the pavement surface. The advantages of grooving are: reduced accidents, reduced hydroplaning, reduced splash and spray, faster braking, safer driving, easy to construct, economical and no adverse effect on pavement fatigue life.
Application(s)
Bridge, City/Municipal, Highway
Technique(s)
Diamond Grooving
Issue(s)
Friction/Safety
Quick Facts: Conventional Diamond Grinding
Conventional diamond grinding (CDG) removes a thin layer of hardened concrete surface using a self-propelled machine outfitted with a series of closely spaced diamond saw blades. CDG provides several benefits: Smooth riding surface , its safe , quiet, removes faulting at joints and cracks, does not significantly affect fatigue life, can extend pavement service life by decades, does not affect overhead clearances underneath bridges or signs, may be done in isolated areas as needed and during off-peak hours and its cost effective.
Application(s)
Airport/Airfield, Bridge, City/Municipal, Highway, Industrial, Race Track
Technique(s)
Diamond Grinding
Issue(s)
Friction/Safety, Smoothness, Tire/Pavement Noise