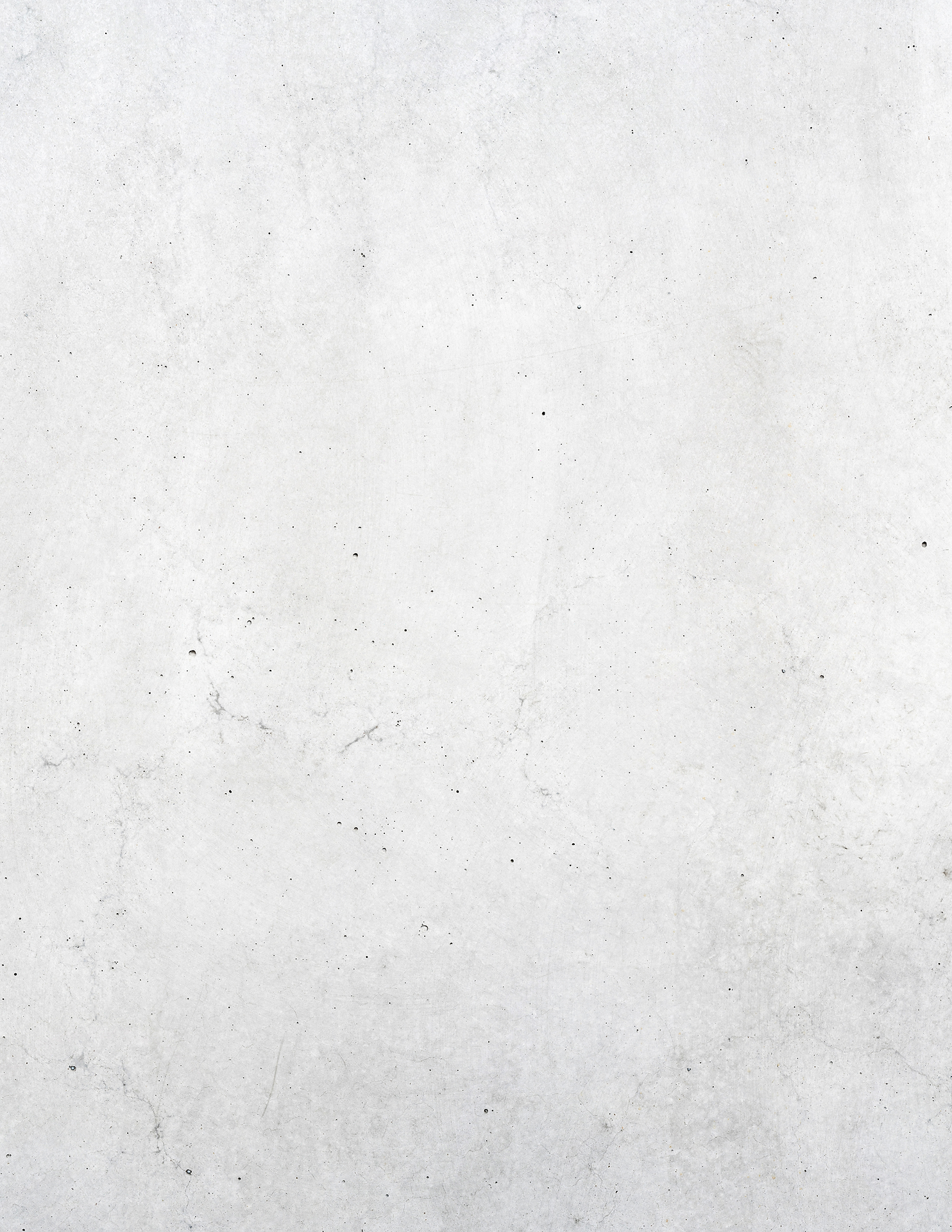
The IGGA offers case studies on pavement surfacing techniques and preservation/repair methods. Select the application(s), preservation/optimization technique(s) or pavement criteria/issue(s) to browse the case studies, or use the search function.
No results found. Please try another combination of categories.
NGCS Provides Alternative Noise Reduction Solution
Next generation concrete surface (NGCS) is the quietest non-porous concrete pavement surface available, providing a solution for noise control in areas where noise walls are not feasible.
Application(s)
Highway, City/Municipal
Technique(s)
Next Generation Concrete Surface (NGCS)
Issue(s)
Tire/Pavement Noise, Friction/Safety
Diamond Grinding Roller Compacted Concrete Pavement
Santa Fe Springs, California, achieved smooth, long lasting pavements with short construction with the use of diamond grinding to create a smooth, quiet surface on roller-compacted concrete pavement (RCC). The project involved replacing damaged asphalt on Greenstone Avenue and Sunshine Avenue, achieving a 25-plus-year pavement life.
Application(s)
City/Municipal, Industrial
Technique(s)
Diamond Grinding
Issue(s)
Smoothness
Diamond Grinding Speeds Asphalt Paving Construction Process
Smoother asphalt installations on SC 544 in Conway, South Carolina were achieved with the application of diamond grinding. The project involved a five-inch mill and overlay conducted in a single-lift operation, where diamond grinding was employed to create an ultra-smooth, high-friction and quiet riding surface. This technique significantly reduced the International Roughness Index (IRI) measurements, improving rideability and safety.
Application(s)
Highway
Technique(s)
Diamond Grinding
Issue(s)
Friction/Safety, Tire/Pavement Noise
Dowel Bar Retrofit for Thin Section Pavements
County Highway 22 in Olmsted County, Minnesota, was successfully restored through the implementation of DBR as a concrete pavement preservation technique. DBR involves installing dowel bars to restore load transfer across joints and cracks, effectively linking adjoining slabs, leading to improvements in pavement performance and extending the service life of the roads.
Application(s)
City/Municipal
Technique(s)
Diamond Grinding, Dowel Bar Retrofit
Issue(s)
Smoothness, Structural/Material Issues
CPR: Rebuilt to Last: Runway and Taxiway Pavement Improvements in DeKalb County, Georgia
A 2007 pavement management report on the runway and taxiway pavements at the DeKalb-Peachtree (PDK) Airport in Chamblee, GA, noted significant amounts of cracking in the longitudinal direction of the runway's panels. The project consisted of replacing 125 of the concrete slabs scattered randomly throughout the 6,001 by 100 foot runway, diamond grinding and then re-grooving the entire surface, as well as re-marking. In total, the repairs included 9,500 square yards of patching; 80,000 linear-feet of joint resealing and crack sealing; 70,000 square yards of diamond grinding; and 56,000 square yards of grooving.
Application(s)
Airport/Airfield
Technique(s)
Diamond Grinding, Diamond Grooving, Full & Partial Depth Repair, Joint and Crack Resealing
Issue(s)
Structural/Material Issues
CPR: Rebuilt to Last: FDR Ramp at RFK Bridge, Manhattan, NY
The Franklin D. Roosevelt (FDR) ramp at the Robert F. Kennedy (RFK) Bridge in Manhattan, NY, was in need of surface repairs. The solution came in the form of longitudinal grooving of the pavement. The project involved milling, paving and grooving.
Application(s)
City/Municipal
Technique(s)
Diamond Grooving
Issue(s)
Friction/Safety